-
BLACKOUT TECHNOLOGIES TARGETS TELEMATICS-INTEGRATED MOBILE DEVICE BLOCKING TO COMBAT SMARTPHONE DISTRACTION - 2 hours ago
-
Sparck Technologies awarded Royal designation - March 27, 2025
-
OpenADR Alliance announces first OpenADR 3.0 certified products with EVoke Systems, E.ON Energy and Universal Devices - March 25, 2025
-
Growing fulfilment and contract packer appoints new Managing Director - March 25, 2025
-
When is it time to invest in a WMS? Understanding the key trigger points - March 25, 2025
-
eCapital helps Vantage Recruitment on its journey to financial success - March 24, 2025
-
Hugo Beck Celebrates 70 Years of Packaging Innovation with Open House Events - March 20, 2025
-
PROLOG FULFILMENT SUPPORTS LUNA DAILY’S COMMITMENT TO BETTER BODY CARE FOR ALL WOMEN - March 19, 2025
-
Motion Ventures launches largest-ever maritime tech fund at $100M to meet the industry’s new pace of adoption - March 18, 2025
-
ITD GLOBAL APPOINTS GROUP CHIEF REVENUE OFFICER - March 17, 2025
Combilift’s wide range of multidirectional forklifts, pedestrian stackers, Aisle Master articulated trucks and straddle carriers has enabled thousands of customers around the world to achieve safer, space saving and more productive handling and storage procedures. Alongside these innovative products, a free service that has long been offered by the Irish manufacturer is a warehouse layout and material flow consultation to ensure that customers make the best possible use of their space – one of their most precious commodities. In the current circumstances when businesses face the challenges of implementing social distancing, advice from Combilift’s team of design engineers is more valuable than ever.
Speaking during a recent virtual press conference Martin McVicar, CEO and co-founder of Combilift, outlined the company’s new approach which uses technology to replace personal site visits to enable customers to continue to benefit from Combilift’s expertise at a time when space optimisation is crucial.
Overcoming challenges for manufacturers
One consequence of the Coronavirus for Combilift’s customers in the manufacturing sector in particular has been the challenge to get back to normal output levels whilst creating extra space in production areas so that employees maintain safe distances from each other. Combilift’s expertise in the design and layout of premises can help overcome these challenges by maximising the production areas – which is where profit is made, whilst reducing the space for storage of raw materials and finished products – which engenders costs. By optimising both these areas companies can comply with safety requirements whilst maintaining output.
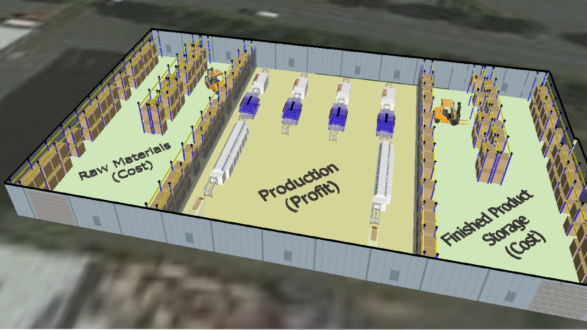
Virtual and digital consultation
Combilift’s free design and layout service has always been a great tool for resolving problems for customers and enabling them to maximise space. These were previously carried out by technical personal visits but have now been replaced with a remote system.
Using in-house developed technology as well as WhatsApp calls with customers whilst they walk around the premises and take shots of specific areas, Combilift design engineers can get a good overview of requirements. Using measurements supplied by clients they can supply 3-D designs and animations within a very short time frame. “We have seen a much increased take up of this free warehouse service,” said McVicar. “Many companies are not encouraging vendor visits but they are making time available to communicate with us. Within 24 hours of speaking to a customer we can produce a 3D design.”
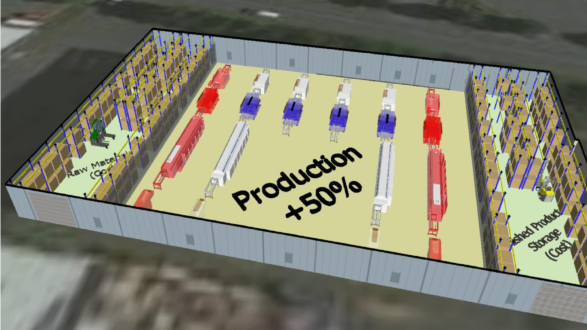
Safety measures at the manufacturing plant.
To ensure continued production, Combilift has introduced a two-shift system instead of its traditional one shift operation. This means that there are only around 350 employees per shift on site in the 46,500m² manufacturing facility. It has also segregated the plant into 8 segments. Employees are scanned by thermal cameras when they arrive on site and if their temperature is above normal this is signalled to the HR department as well as the employee. Clocking in is now done via a touchless key fob and doors are kept open whenever possible. Those that cannot remain permanently open have been fitted with copper coatings which significantly reduces the time that a virus can be harboured on the surface compared to steel. There are multiple hand sanitizers strategically placed across the whole facility, floor markings indicate the 2m distance to be maintained by employees and it is mandatory to wear face masks. The company has closed its main hot canteen and has opened smaller canteens in the eight new factory segments. “I give regular updates by video instead of the personal staff assemblies that we previously did every six weeks and this ongoing communication ensures that employees are continually informed and therefore understand that the measures we are taking are in everyone’s best interests,” said McVicar.
See a video of the measures that Combilift has implemented here: